0-1000g ... 0-50 Kg (0-10N ... 0-500N) = Standard Range (SR)
The Honigmann RFS® 60 is a single roll tension sensor designed to measure the running line tensions of yarn, wires, optic fibers, cables, tapes, bands, wraps, webs, foils and similar process materials. Existing rollers with 20-180 degree wrap angles can be converted for use as RFS measurement locations.
The RFS features a unique strain-gauge design delivering extremely precise and stable measurements while providing maximum overload protection. RFS sensors are used in a variety of low and high-range applications, such as measuring 1 or 2 grams on fine denier yarns/fibers to measuring wire/cable up to 50Kg / 5000 N / 110 lbs.
High precision mechanical design ensures the calibrated accuracy of the RFS remains unchanged throughout the sensor’s service life. The measurement is not influenced by the force introduction point, i.e. the sensor is not affected by lever arm action or any axial tilt torques which might occur.
Measurement Principle
The force acting radially at the bearing journal, along the measurement vector, causes a microscopically small, elastic deformation of the complex load cell. This deformation is registered at a pre-determined position by way of strain gauges and is then evaluated electronically. The high mechanical stiffness of the load cell enables measurement with virtually no excursion. This tension measurement principle is based on the evaluation of the force applied radially and transferred to the sensor by way of the bearing journal. This force is determined by the reversing geometry and the line tension.
- ultra compact and small design: for 16mm mounting hole, total length incl. angled connector only 54mm (bearing journal dia. 5mm)
- existing reversing points can be adapted as measurement points
- overload protection up to 800%
- independent of the force introduction point, i.e. the sensor is not affected by lever arm action
- no influence of any axial tilt torques or direct axial forces which might appear
- centrifugal force will take no affect with optimal alignment in rotating purposes
- robust, stainless steel housing
- thought-through concept of housing for simple mounting
- suitable to design small measuring rollers
Model | Capacity (Resultant Force) | Bearing Journal Diameter (mm) | Range Type |
---|---|---|---|
RFS150-2N | 200 g / 2 N / 0.44 lbs | 5, 8 or 10 mm | LR |
RFS150-3N | 300 g / 3 N / 0.66 lbs | 5, 8 or 10 mm | LR |
RFS150-4N | 400 g / 4 N / 0.88 | 5, 8 or 10 mm | LR |
RFS150-5N | 500 g / 5 N / 1.1 lbs | 5, 8 or 10 mm | LR |
RFS150-10N | 1 Kg / 10 N / 2.2 lbs | 5, 8 or 10 mm | SR |
RFS150-20N | 2 Kg / 20 N / 4.4 lbs | 5, 8 or 10 mm | SR |
RFS150-30N | 3 Kg / 30 N / 6.6 lbs | 5, 8 or 10 mm | SR |
RFS150-40N | 4 Kg / 40 N / 8.8 lbs | 5, 8 or 10 mm | SR |
RFS150-50N | 5 Kg / 50 N / 11 lbs | 8 or 10 mm | SR |
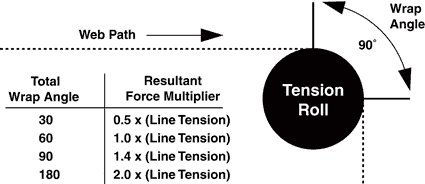
Measuring Principle | Strain Gauge |
Accuracy | ±0.5% Full Scale or better |
Sensor Excitation | 10 VDC (12 VDC, max.) |
Sensor Output | 1.5 mV/V |
Input Resistance | 350 Ohms |
Output Resistance | 350 Ohms |
Overload Protection | 400 - 800% |
Deflection | 0.07mm (max.) |
Housing Material | Stainless Steel |
Environmental Protection | IP50 (Splash-Proof) |
Cable Type | 4.5 mm diameter shielded cable with bare leads |
Cable Length | 3 meter / 10ft standard, longer lengths available, inquire |
Operating Temperature | 15 to 155° F (-10 to 70° C) |
Fequency Responce | 5 msec (200 Hz) |
Resultant Force | [Line Tension] x sine α [wrap angle] |
Mass | 400g (approximate) |
Thank You
Thank you for your quote request, we will contact you within 1-2 business days.